About us
FAQ Testing and Technical Articles
We get a lot of questions regarding different tests and test procedures.
We have listed the most common questions from our customers below.
Customer service
If you can not find the answer you are looking for here, please, contact our service and support team.
Are you interested in conducting a test?
Our corrosion test experts will be happy to assist you every step of the way.
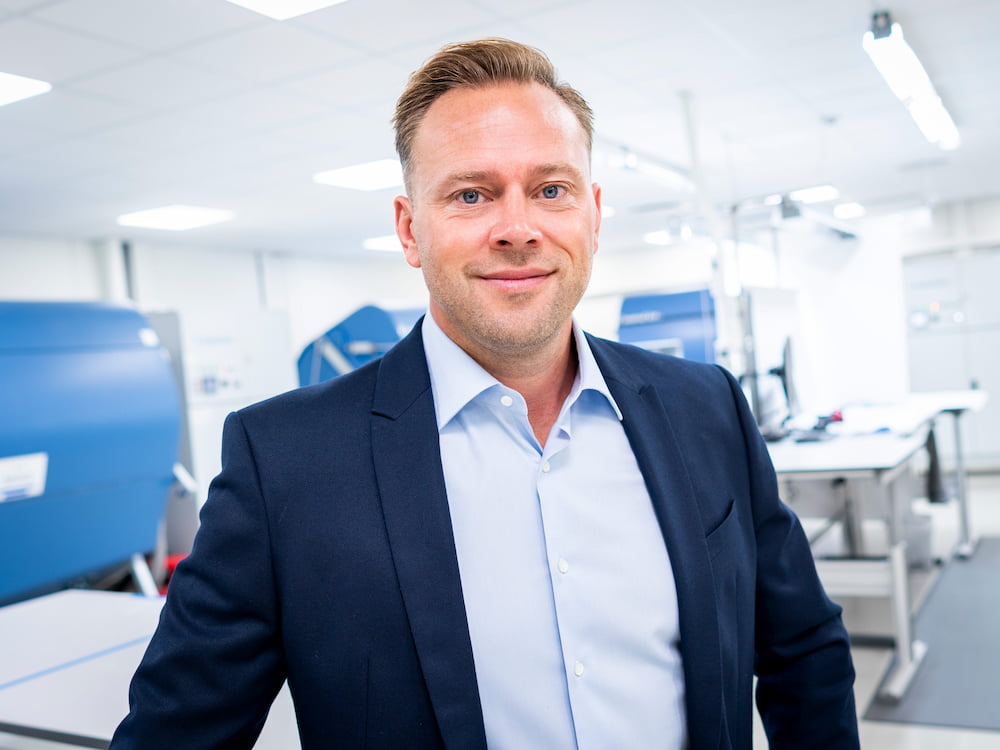
Joakim Ekström
Sales & Market Manager / Senior Test Engineer
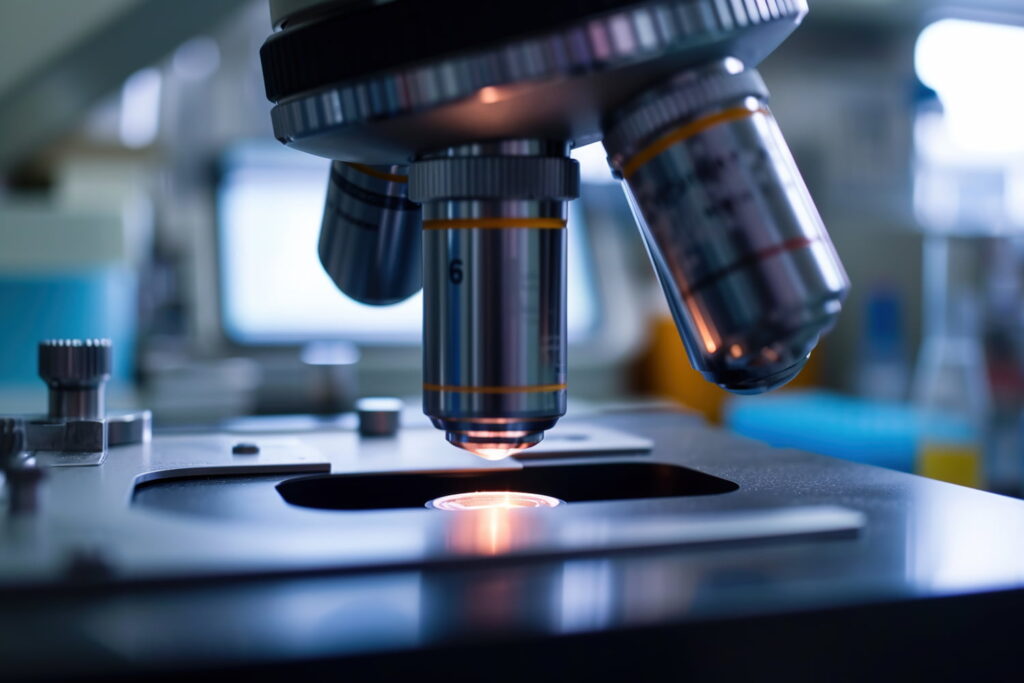
Our services
What are your needs? We have extensive expertise in what OEMs require and the
standards they demand.
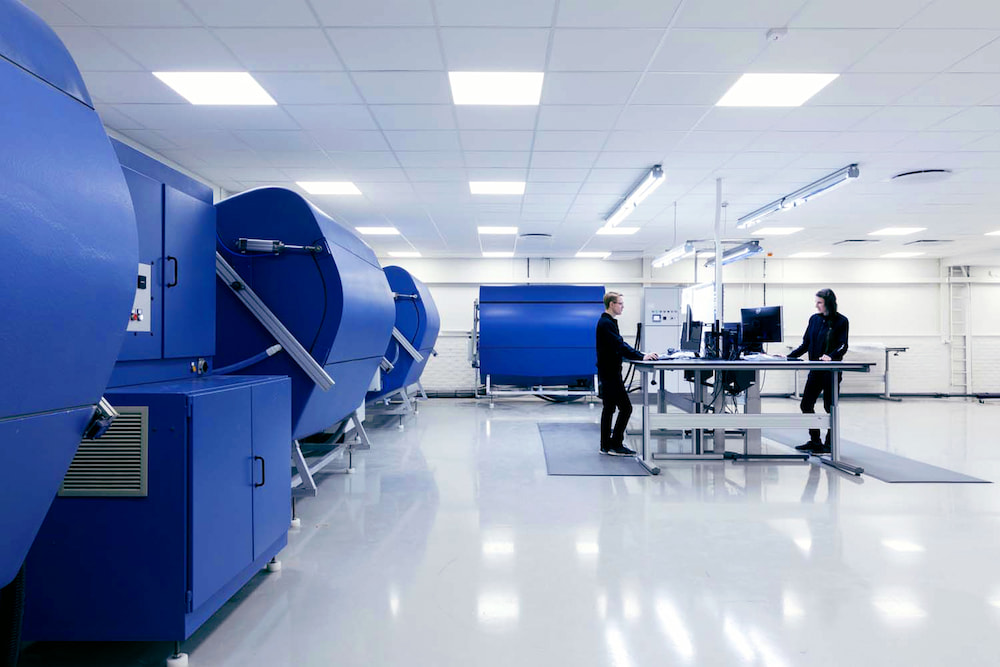
Laboratory and equipment
Cotec Labs provides a 1200 sqm laboratory facility. Take a closer look at our laboratory
and equipment.
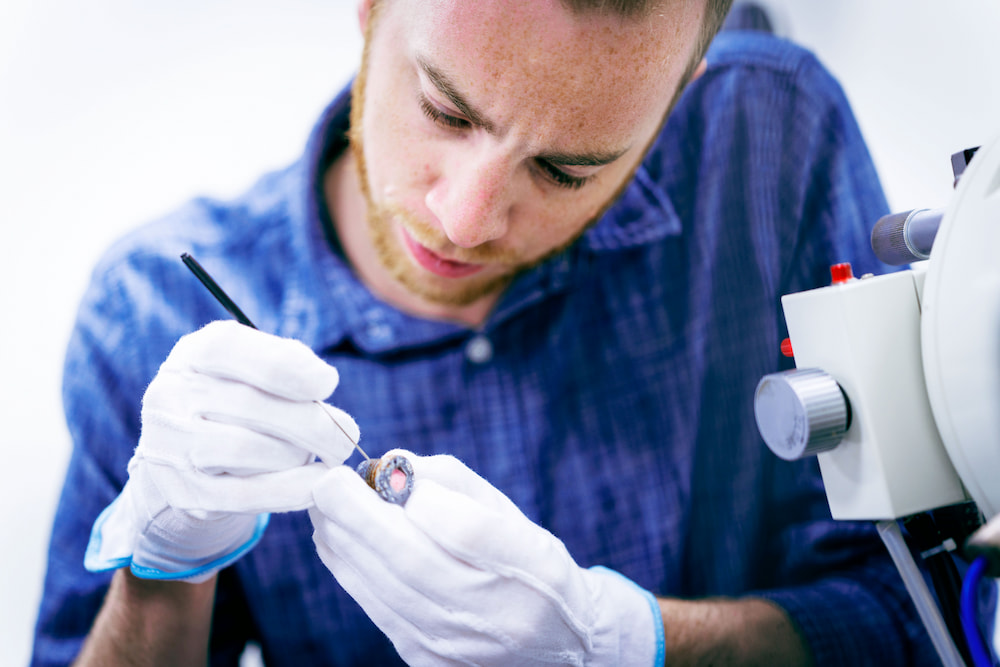
Quality and certificates
We are accredited by Swedac and part of the international accreditation network ILAC.