Technical article
Cyclic corrosion testing
Introduction to Cyclic Corrosion Testing
In the evolution of materials science, cyclic corrosion testing represents a significant part in evaluating the corrosion resistance of materials and coatings. Unlike conventional steady-state exposure tests, many cyclic methods offer a more realistic methodology by simulating real-world environmental conditions through accelerated corrosion tests.
Controlled temperature is crucial in cyclic corrosion testing to accurately simulate real-world conditions and assess the long-term durability of materials under different climates, thereby enabling manufacturers to predict product longevity.
When exposing test samples to varying conditions, cyclic corrosion testing better represents the complex corrosive processes materials face in field of use. What it significantly means is that cyclic corrosion testing involves exposing samples to alternating wetting and drying, often incorporating salt spray or salty acidified rain with a humidity setting relative to the fluctuating temperature. This approach really shows the limitation of conventional salt spray tests where a steady state of humidity, fixed temperature or both is the case. The conventional methods then fail to account for the natural alternate between different environmental states.
What is Cyclic Corrosion Testing?
Cyclic corrosion testing (CCT) is a sophisticated method designed to accelerate the occurrence of real-world corrosion failures under controlled laboratory conditions. This testing approach is invaluable for predicting and understanding potential corrosion issues that materials and coatings might face in actual service environments. Unlike traditional methods, CCT exposes samples to a series of alternating wet and dry conditions, often incorporating salt solutions and acidified rain, with humidity settings that fluctuate relative to temperature changes. This dynamic simulation provides a more accurate assessment of how materials will perform in real-world scenarios, making it a crucial tool for industries such as automotive, aerospace, military, offshore, paint, plastics, packaging, and electronics. By replicating the complex interplay of environmental factors, CCT helps industries ensure the durability and reliability of their products.
The old habits of constant climate testing
It all started at the beginning of the 20th century. An ancient test method where salt fog was sprayed onto the test specimens under constant conditions and temperature. Salt fog testing played a crucial role in traditional methods, particularly in the context of ASTM B117 procedures. ASTM B-117 was born and for a long time looked completely unchanged in its design. The salt content in the applied electrolyte was in its cradle, 25% NaCl. In the following decades, the method was changed by lowering the salt content to today’s level, at 5% NaCl.
The traditional salt spray test was revolutionary as you could “get answers” to what was a fully protected metal and what lacked full protection. Compared to before, the introduction of the method meant a revolution in terms of quality, while in recent times new insights have been gained. Today, the vast majority of researchers agree that synthetic weathering-like cyclic corrosion test methods should dominate results-based quality research regarding corrosion and corrosion-protective coatings.
The constant state methods are vague or even faulty in response to the proposed behavior, and what the corrosion mechanisms materials typically experience during their life cycle. The methods featuring constant corrosion tests like salt spray may be repeatable as their nature is simple. Though repeatability has little to do with significance. It all comes down to the real purpose of the test. When verifying the quality of any coating it is for a fact the intended environment in the field of use that makes the method reliable.
Comparison with traditional methods
Cyclic corrosion testing represents a significant advancement over traditional salt spray testing. While conventional salt spray tests maintain a steady-state environment, CCT simulates real-world conditions by varying temperature and humidity levels. This dynamic approach allows CCT to more accurately predict real-world corrosion failures, providing a comprehensive evaluation of various corrosion mechanisms, including general corrosion, galvanic corrosion, and crevice corrosion. Traditional salt spray testing, on the other hand, is limited in its ability to replicate the complex environmental conditions that materials face in actual use. By offering a more realistic simulation of outdoor exposure, CCT delivers more reliable and relevant results, making it a superior method for assessing corrosion resistance.
The advantages of Cyclic Corrosion Testing
Mimicking natural environmental conditions more accurately will lead to more realistic assessments of corrosion mechanisms and material degradation. The relative corrosion rates of structures, and morphologies observed in accelerated cyclic tests tend to mirror those found in real-world scenarios more accurately than steady-state methods. Pattern accelerated laboratory tests provide realistic simulations by mimicking wet and dry cycles, thereby offering better correlations to outdoor corrosion rates and mechanisms compared to traditional salt spray tests. This improved correlation makes cyclic testing particularly valuable for industries where long-term material performance is critical, such as automotive, aerospace, military and marine applications.
The primary goal of cyclic corrosion testing is to achieve accelerated testing results that more closely correlate with outdoor exposure outcomes. Correlation is a key factor that is already argued for, and the time factor is the second parameter where acceleration grant laboratory testing in favor of onsite exposure which is ineffective and time-wasting.
Another key aspect of cyclic corrosion testing lies in its ability to evaluate various corrosion mechanisms simultaneously. This itself is time-effective, and by replicating the complex interplay of environmental factors, these tests can assess general corrosion, galvanic corrosion, edge corrosion, propagation from scribe, and crevice corrosion within a single test cycle. When this broad spectrum of evaluation aspects is met manufacturers and researchers obtain a more universal understanding of a complex component, its protective coatings, and material’s corrosion behavior in significant surroundings.
Test Methods and Procedures
Cyclic corrosion testing involves a series of procedures designed to replicate real-life environmental conditions within a controlled laboratory setting. Test subjects are exposed to various conditions, including alternating wet and dry phases, salt spray, and fluctuating temperatures, within an enclosed chamber. This chamber can cycle through different environmental states, accurately simulating the conditions that materials and coatings encounter outdoors. CCT machines are capable of testing for a range of corrosion mechanisms, such as general corrosion, galvanic corrosion, and crevice corrosion. The procedures for CCT are outlined in several industry standards, including ASTM G85, ASTM G44, and ASTM D5894, ensuring consistency and reliability in testing.
Deeper insights into Cyclic Corrosion Testing?
Cyclic corrosion testing (CCT) are methods designed to predict and understand potential real-world corrosion failures. Unlike traditional tests, generally Salt spray tests, CCT simulates natural environmental conditions by displaying test subjects to a variation of different scenarios. The salt spray phase is a specific part of the CCT process that simulates conditions similar to traditional salt spray testing but for a shorter duration. It involves exposing samples to alternating wetting and drying, often incorporating salt solutions, and acidified rain with a humidity setting relative to the fluctuating temperature. This superior approach mimics real-life situations that materials and coatings encounter outdoors, providing a more accurate assessment of their durability and performance.
Cyclic corrosion testing is suitable for comparative testing in the optimization of surface treatment systems, articles and components. It is a universal methodology when it comes to testing complex products- and geometries.
Particular methods that are used are; PSA VW PV1210, Jaguar Land Rover TPJLR.52.265, Volvo Trucks ACT 423-0014, Volvo Cars ACT 2 1027, 1449, Ford Cyclic CETP 00.00 L-467 and Scania Accelerated Cyclic Corrosion Tests ACT 4319/ACT2 STD4445.
Mercedes, Toyota and many other OEMs have the same approach when it comes to testing though the actual climate cycle can vary a bit between the OEMs as well as the assessments.
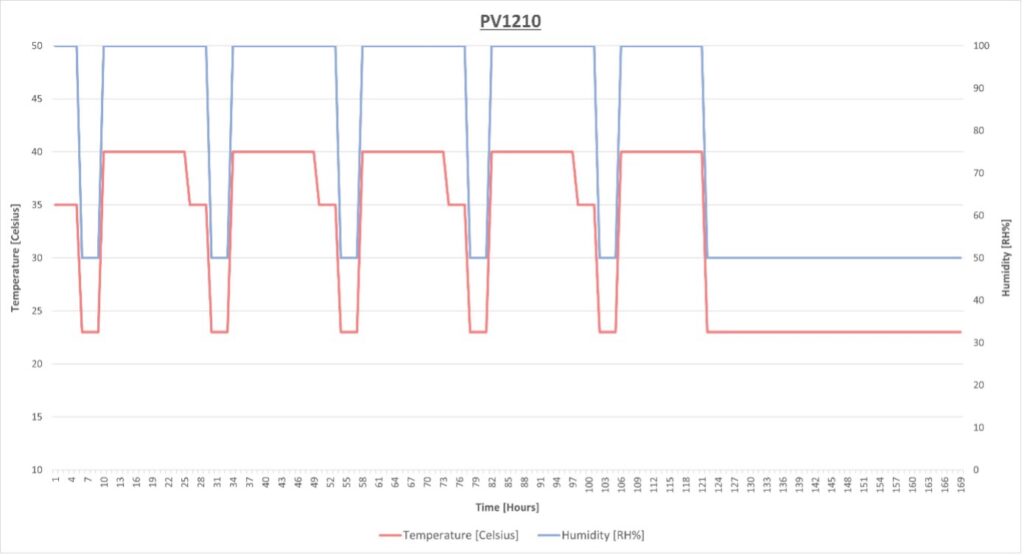