About us
What is UV Testing?
A UV test typically refers to a test that measures the effects of ultraviolet (UV) radiation on materials, products, or biological samples. These tests, known as UV exposure testing, are commonly used in various fields, such as material testing. This means evaluating how materials like plastics, paints, and coatings withstand UV exposure, which can lead to degradation, discoloration, or loss of mechanical properties.
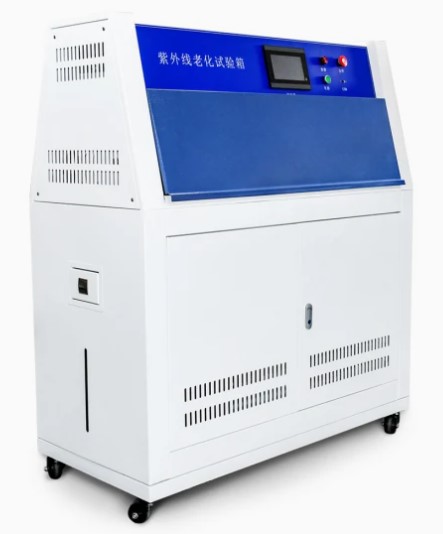
How do you test for UV protection?
Testing for UV protection involves several methods, depending on the context (like materials, cosmetics, or clothing). UV Testing simulate long-term UV exposure using specialized machines (e.g., Xenon arc testers) to assess how materials like plastics or coatings degrade over time. Outdoor exposure is crucial in UV testing as it replicates real-world conditions, including UV light and moisture, to evaluate durability and photodegradation.
What is accelerated UV testing?
Accelerated weathering testing, including accelerated UV testing, is a method used to evaluate how materials will perform when exposed to ultraviolet (UV) light over time. This testing simulates long-term exposure to sunlight, helping manufacturers predict how their products will degrade, discolor, or lose mechanical properties.
Key aspects of accelerated UV testing
Purpose
- Assess the durability and stability of plastics when exposed to UV radiation, which can lead to issues like brittleness, fading, and loss of strength.
Testing Equipment
- Xenon Arc Testers: These devices use xenon arc lamps to simulate sunlight, including both UV and visible light, in a controlled environment.
- Fluorescent UV Lamps: These replicate UV exposure from natural sunlight, often used for shorter-duration tests.
Testing Conditions
- Temperature and Humidity Control: The tests often include controlled temperature and humidity to mimic real-world conditions.
- Cycle Duration: The testing may involve alternating periods of UV exposure and moisture condensation to simulate the effects of environmental conditions.
Assessment Metrics
- Color Change: Measuring changes in color using spectrophotometry to assess discoloration.
- Mechanical Properties: Evaluating changes in tensile strength, flexibility, and impact resistance before and after exposure.
- Visual Inspection: Observing surface defects, crazing, or other forms of degradation.
Standards
- Various industry standards (like ASTM G154 or ISO 4892) provide guidelines for conducting these tests and interpreting the results.
Benefits of accelerated UV-tests
- Predictive Insights: Helps manufacturers identify potential issues before products reach the market, allowing for improvements in formulation or protective additives.
- Quality Assurance: Ensures that products meet durability and performance standards, enhancing customer satisfaction.
Accelerated UV testing is crucial for ensuring that products remain reliable and visually appealing over their intended lifespan.
Applications of UV testing
UV testing has a wide range of applications across various industries, each benefiting from the insights provided by these tests.
Materials testing
UV testing is important for evaluating the durability and performance of materials such as plastics, coatings, and textiles. It helps in understanding how these materials will withstand prolonged UV exposure.
Product development
During product development, UV testing is used to create new materials and products that can endure the effects of UV light. This ensures that the final products are robust and long-lasting.
Quality control
UV testing is an integral part of quality control processes, ensuring that products meet the required standards and can withstand UV exposure without significant degradation.
Research and development
In research and development, UV testing is used to study the effects of UV light on various materials. This research can lead to the development of new technologies and materials with improved UV resistance.
Automotive
In the automotive industry, UV testing is used to assess the durability and performance of materials used in vehicle interiors and exteriors. This ensures that automotive components remain reliable and visually appealing over time.
UV test standards
UV test standards provide guidelines and procedures for assessing the effects of ultraviolet (UV) radiation on various materials, products, and biological samples. Here are some key standards commonly used in different industries:
1. ASTM Standards
ASTM G154: Standard Practice for Operating Fluorescent Light Apparatus for UV Exposure of Nonmetallic Materials. This standard outlines the conditions for using fluorescent UV lamps to simulate sunlight.
ASTM G155: Standard Practice for Operating Xenon Arc Light Apparatus for Exposure of Nonmetallic Materials. This standard covers the use of xenon arc lamps for accelerated weathering tests.
ASTM D4329: Standard Practice for Testing the Accelerated Aging of Photovoltaic Modules Using UV Exposure.
ASTM D2565: Standard Guide for Photochemical and Environmental Stability Testing of Polymeric Materials.
ASTM D5208: Standard Practice for Fluorescent Ultraviolet (UV) Exposure of Photodegradable Plastics”
ASTM D5894: Standard Practice for Cyclic Salt Fog/ UV Exposure of Painted Metals (Alternativ Exposure in a Fog/Dr Cabinet and a UV/Condensation Cabinet)
ASTM D6695: Standard Practice for Xenon-Arc Exposures of Paint and Related Coatings.
ASTM D4459: Standard Practice for Xenon-Arc Exposure of Plastics Intended for Indoor Applications.
2. ISO Standards
ISO 4892: Plastic—Methods of Exposure to Laboratory Light Sources. This series includes various parts that specify methods for testing plastic materials under UV exposure.
ISO 10006: Guidance on the management of quality in projects, which includes considerations for durability testing.
ISO 10683: Plastic—Test Method for the Effects of UV Radiation on the Long-Term Durability of Paints and Coatings.
ISO 16474: UV Exposure Test
3. IEC Standards
IEC 61215: Photovoltaic (PV) module design qualification and type approval, which includes UV exposure tests as part of the durability assessment.
4. AATCC Standards
AATCC Test Method 183: A method for testing the UV protection provided by textile materials, often used in apparel and outdoor fabrics.
AATCC Test Method 16: A method for the assessment of colorfastness to light.
5. Other Relevant Standards
EN 15978: European standard for assessing the environmental performance of buildings, including considerations for UV exposure on building materials.
SAE J2412: Accelerated Exposure of Automotive Interior Trim Components Using a Controlled Irradiance Xenon-Arc Apparatus.
SAE J2527: Performance Based Standard for Accelerated Exposure of Automotive Exterior Materials Using a Controlled Irradiance Xenon-Arc Apparatus.
FDA Guidelines: For testing sunscreens and cosmetics, including methods to measure SPF and UVA protection.
These standards help ensure consistency, reliability, and safety in testing procedures, allowing for meaningful comparisons across different products and materials. Compliance with these standards is crucial for manufacturers to meet regulatory requirements and provide consumers with safe and durable products.
If you need more details on a specific standard or its application, feel free to ask!
How much does accelerated UV testing cost?
The cost of accelerated UV testing can vary widely depending on several factors, including:
Type of Testing
Different methods (e.g., xenon arc testing, fluorescent UV testing) have varying costs due to equipment and procedures.
Material or Product
Testing costs can differ based on the complexity of the material or product being tested.
Duration of Testing
Longer exposure times or multiple test cycles will increase costs. Standard tests might run for a few hundred to several thousand hours.
Reporting and Analysis
Comprehensive analysis and reporting of results can add to the cost, especially if detailed recommendations or modifications are included.