Methods & requirements
ISO 9227 Corrosion Test (Salt Spray)
Corrosion testing determines the resistance of materials to corrosion under specific environmental conditions, like temperature and humidity. Other accelerating factors can be presence of chemicals and the pH-level of the salt fog and pluviometry.
There are mainly two different types of corrosion test standards, field performance and accelerated corrosion tests. Cotec Labs is focused on different types of standardized corrosion tests.
What is important when choosing a test method is to make sure the controlled environment matches the natural outside environment in terms of behaviour of the protective coating when it degrades. Since the methods used in a laboratory environment are accelerated, studies must underpin the extrapolation of test duration.
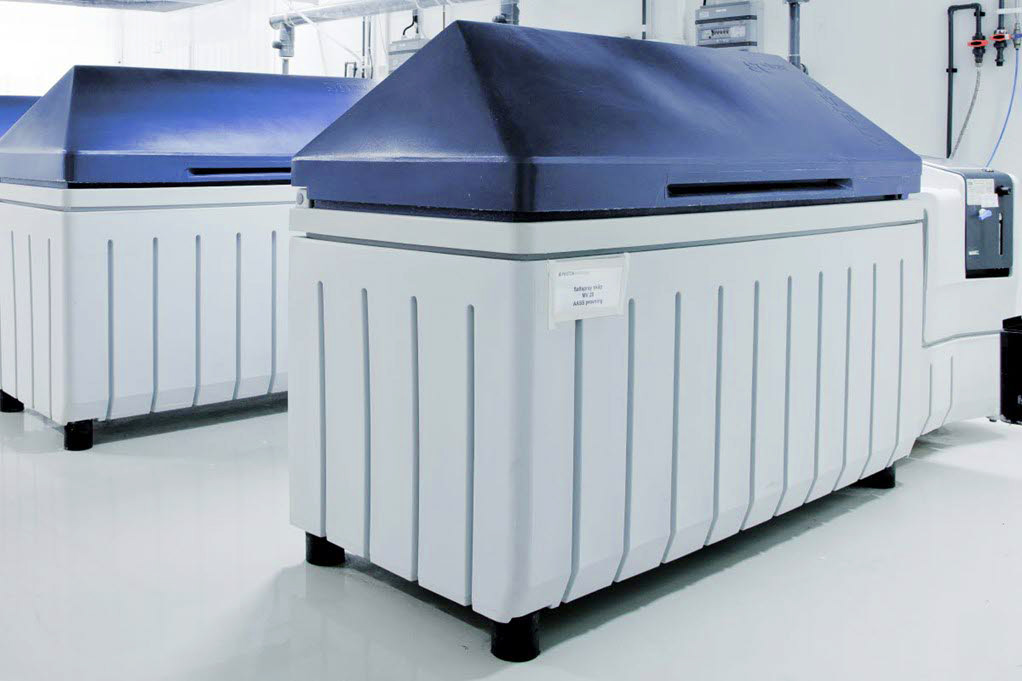
What is standard ISO 9227? (Salt Spray)
ISO 9227:2022 is the latest iteration of a long-established standard that originated to standardize the procedures for assessing the long-term corrosion resistance of metallic materials and protective metallic coatings. The standard is developed and maintained by the International Organization for Standardization (ISO), which is a globally recognized body for setting international standards. ISO 9227 has evolved over the years to keep pace with advancements in material science and industry requirements.
Quality Assurance: One of the primary purposes of ISO 9227:2022 is to ensure the quality and durability of materials and coatings. This is especially critical in industries where products are exposed to harsh environments or conditions, such as marine, aerospace, and automotive industries.
Comparability: ISO 9227:2022 provides a standardized method for comparative testing materials and conversion coatings, making it possible to compare the corrosion resistance of different products or materials. This is essential for manufacturers, as it allows them to select the most appropriate materials for their specific applications.
Research and Development: Researchers and engineers use ISO 9227:2022 as a tool to evaluate and improve the temporary corrosion protection of materials and organic and inorganic coatings. It helps in developing new materials that can withstand corrosive environments more effectively.
Procedure for testing according to ISO 9227 (Salt Spray)
The core of ISO 9227:2022 is the salt spray test, which simulates the corrosive effects of a salt-laden atmosphere. The test chamber used in this standard creates a controlled environment where a saline solution is atomized and sprayed onto the test specimens. There are three different types of artificial atmospheres salt spray test methods: Neutral Salt Spray NSS test, (accelerated) Acetic Acid Salt Spray AASS test and Copper Acetic Salt Spray CASS test (acid salt spray CASS test). NSS test uses 5% saline (natrium /sodium) solution with neutral pH (6.5-7.2), AASS test uses 5% saline solution with lower pH (3.1-3.3) and CASS test uses a 5% saline solution with lower pH (3.1-3.3) but with copper chloride dihydrate (concentration of 0.26g/l ±0.2g/l).
Here are the key steps involved in conducting salt spray tests according to ISO 9227:2022:
Exposure to Salt Spray: The prepared test specimens are placed inside an ISO 9227 salt spray test chamber with a specific test cabinet environment. The chamber is then filled with a salt solution (sodium) (neutral salt spray test NSS, accelerated acetic acid salt spray AASS, or acid salt spray CASS) and a fog of salt-laden water is created by spraying the solution into the chamber. This atmosphere is maintained for a specified period, which can range from hours to weeks, depending on the test conditions.
Evaluation of Corrosion: After the exposure period, the test specimens are removed from the chamber, cleaned, and visually inspected for signs of corrosion. Various evaluation methods, such as rating scales or measurements of corrosion products, may be employed depending on the specific requirements of the test. Client requests can also be involved to check the specific corrosion protection of their product.
Documentation: The results of the salt spray tests are recorded, including details about the test conditions, exposure time, and the appearance of corrosion on the test specimens.
Data Analysis: The collected data is analyzed to determine the corrosion resistance of the materials or coatings being tested. This analysis can involve comparing the performance of different tested material or assessing the suitability of a material for a specific application.
ISO 9227 (Salt Spray) – Relevance in Contemporary Industries
ISO 9227:2022 remains highly relevant in contemporary industries for several reasons:
Environmental Concerns: As industries become more environmentally conscious, the need to develop materials and organic and inorganic coatings that can withstand harsh conditions without corroding is paramount. ISO 9227:2022 aids in the development of eco-friendly, long-lasting products.
Globalization: With the globalization of supply chains, manufacturers must ensure that their products meet international standards. ISO 9227:2022 provides a common benchmark that facilitates trade and ensures product quality.
Advanced Materials: As new materials and organic and inorganic coatings are developed, it is essential to evaluate their corrosion resistance. ISO 9227:2022 helps in assessing the performance of these advanced anodic and organic coatings, ensuring they meet industry standards.
Product Longevity: Consumers and industries alike demand products that last longer and require less maintenance. ISO 9227:2022 helps manufacturers design products that can withstand the test of time.
Safety: In critical applications like aerospace and automotive, safety is paramount. Corrosion can compromise the structural integrity of components. ISO 9227:2022 helps ensure that safety-critical parts are corrosion-resistant.
Uses and factors to consider when using ISO 9227 (Salt Spray)
ISO 9227:2022, which deals with corrosion tests in artificial atmospheres using salt spray, serves several crucial purposes across various industries. Here are some of its primary uses:
Quality Verification: Manufacturers use ISO 9227:2022 to assess the corrosion resistance of materials and coatings to ensure that their products meet the required quality standards. This is essential for industries such as automotive, aerospace, and marine, where durability and safety are paramount.
Test Conditions: ISO 9227:2022 provides guidelines for various test conditions, including the duration of exposure, temperature, and concentration of the salt solution. Selecting the appropriate test conditions that closely resemble the real-world environment is crucial.
Sample Preparation: Proper preparation of test specimens is essential. Surface preparation, including cleaning and pre-treatment, should follow the specified procedures to mimic real-world conditions accurately.
Sample Size and Geometry: The size and geometry of test specimens should be representative of the actual components or materials being tested. Inadequate sample size or geometry can lead to unrealistic results.
Material and Different Coating Systems Selection: Engineers and designers use this standard to compare and select materials and coatings based on their corrosion resistance properties. It aids in making informed decisions about which anodic and organic coatings are best suited for specific applications.
Interpretation of Test Results: Understanding how to interpret the results of the salt spray test is vital. Depending on the application, results may be evaluated based on visual inspection, weight loss, or other criteria specified in the standard. Accurate record-keeping and reporting of test conditions, procedures, and results are essential for traceability and verification. This documentation helps demonstrate compliance with ISO 9227:2022 and provides a basis for future reference.
Repeatability and Reproducibility: It’s essential to ensure that the testing procedure is repeatable and reproducible. This involves verifying that different laboratories or operators can obtain consistent test results using the same conditions and equipment.
Correlation with Real-World Conditions: ISO 9227:2022 provides accelerated corrosion testing. Users should be aware that the results may not perfectly correlate with the performance of materials or coatings in actual outdoor environments. Additional testing or field experience may be necessary for a comprehensive assessment. It is fore example not common to find the outdoor correlation of acetic acid salt spray, which is mostly used to checking testing anodic and/or decorative coatings and the denseness of the coating to avoid corrosion stress due to micro cracks in the coating.
Material Variability: Materials and coatings can vary in their corrosion resistance properties, even within the same specifications. It’s crucial to account for material variability when conducting tests and interpreting results.
Compliance and Certification: Regulatory bodies and certification agencies often require compliance with ISO 9227:2022 to ensure that products meet specific corrosion resistance standards. Compliance can be a prerequisite for market access or industry certifications.
Product Longevity: Manufacturers use salt spray testing to predict the expected lifespan of products and components, or testing anodic and/or decorative coatings, when exposed to corrosive conditions. This is particularly important in industries where product longevity is a key selling point.
Troubleshooting and Failure Analysis: When corrosion-related issues arise in the field, ISO 9227:2022 can be used for troubleshooting and failure analysis. It helps identify the root causes of corrosion-related failures and guides corrective actions.
Environmental Impact: The disposal of salt solutions and waste materials generated during testing should be managed in an environmentally responsible manner in compliance with local regulations.
Safety: Handling salt solutions and operating salt spray test chambers can involve safety considerations, including chemical exposure and electrical hazards. Safety protocols should be followed diligently.
In conclusion, ISO 9227:2022 is a valuable tool for assessing corrosion resistance in materials and coatings, but its effectiveness depends on careful consideration of various factors to ensure accurate and meaningful results. Properly conducted salt spray testing can help manufacturers and industries make informed decisions, improve product quality, and enhance the reliability and longevity of their products.
Our most common corrosion tests
Talk to our corrosion test experts
Are you interested in conducting a test? Feel free to contact us – we’re here to assist you every step of the way.
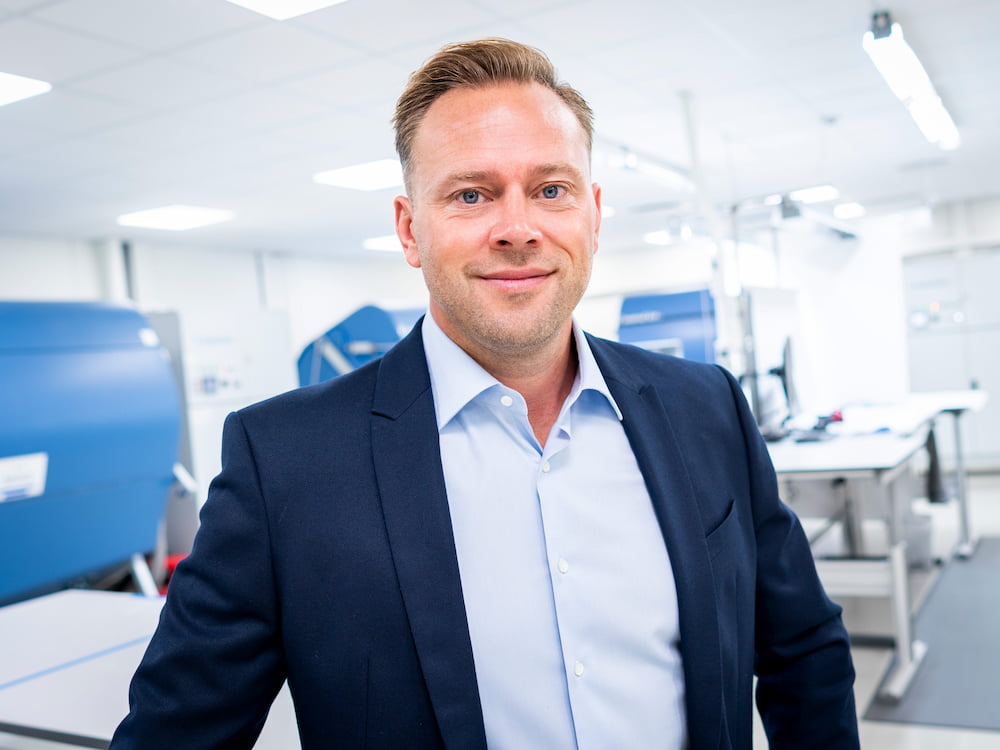
Joakim Ekström
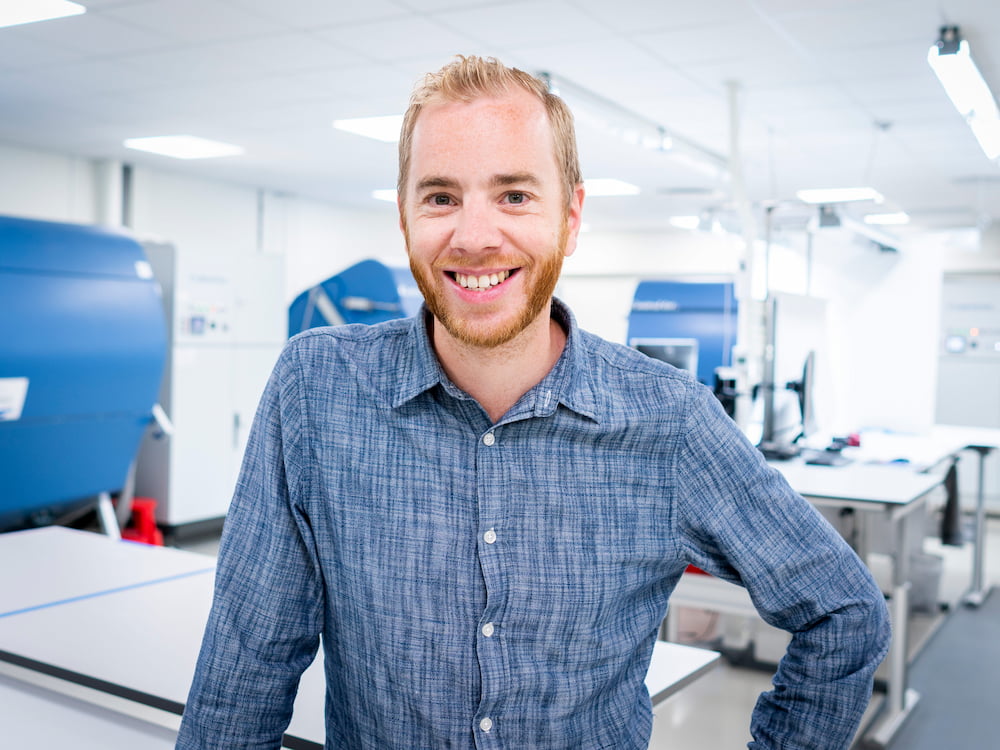
Erik Waltersson
Accredited by SWEDAC
and part of the international accreditation network ILAC
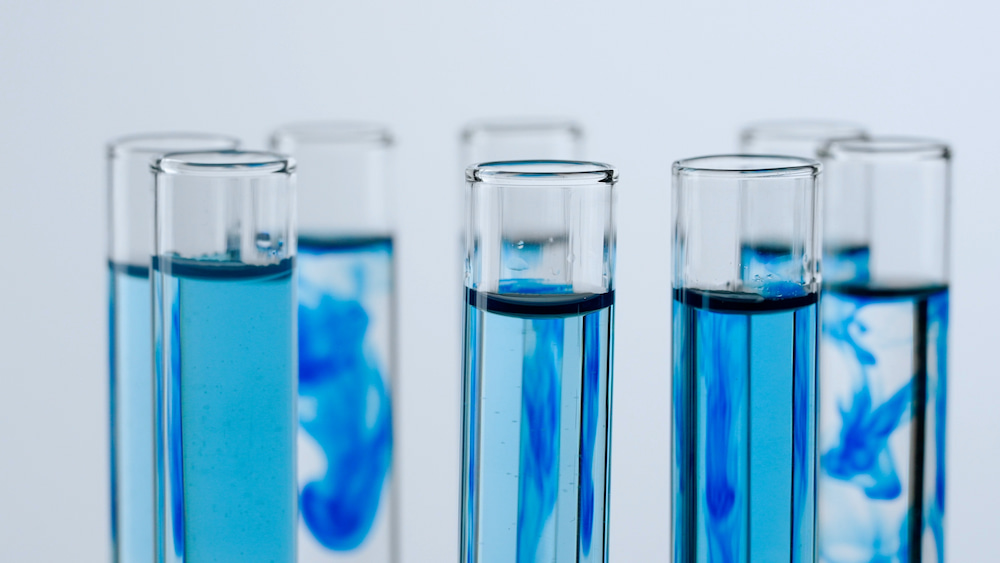
Methods and requirements
We offer a comprehensive and continuously expanding lab-scope of over 300 available test methods and standards.
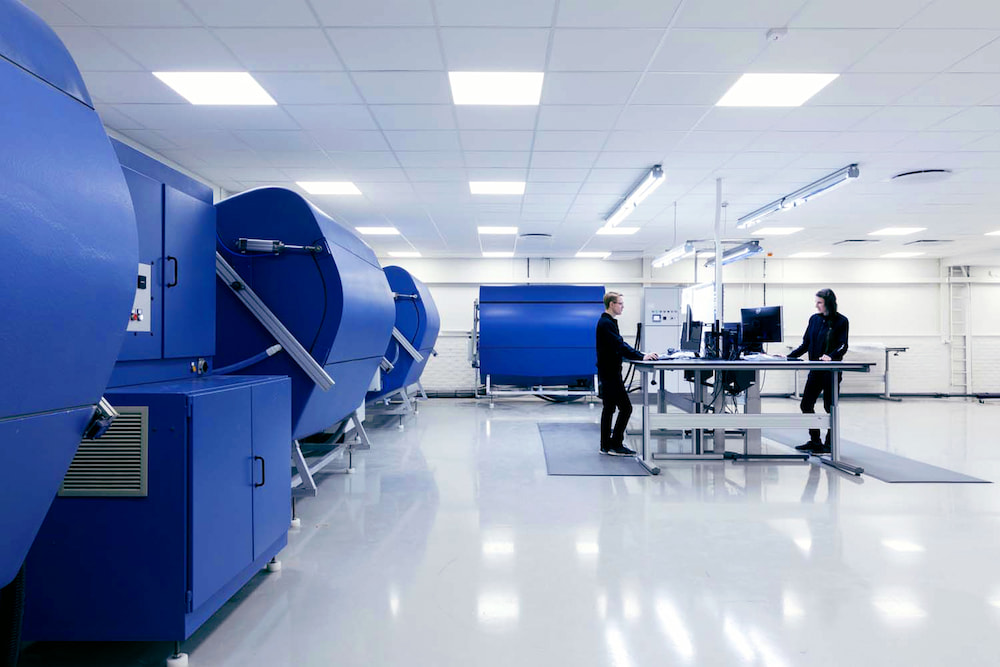
Laboratory and equipment
Cotec Labs provides a 1200 sqm laboratory facility. Take a closer look at our laboratory
and equipment.
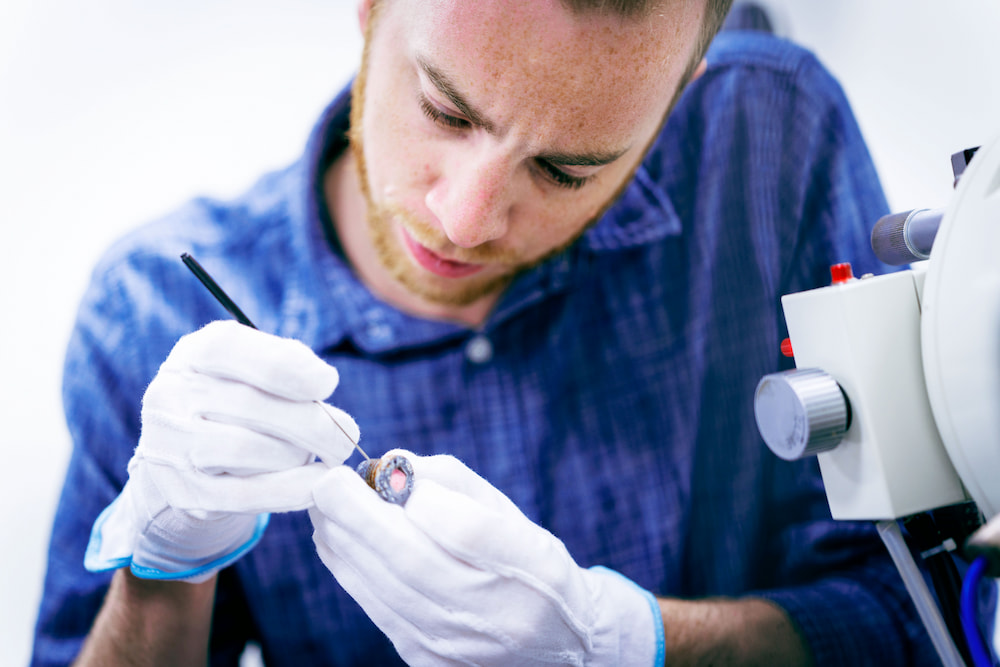
Quality and certificates
We are accredited by Swedac and part of the international accreditation network ILAC.