Methods & requirements
VW PV 1209 Corrosion test
Corrosion testing determines the resistance of materials to corrosion under specific environmental conditions, like temperature and humidity. Other accelerating factors can be presence of chemicals and the pH-level of the salt fog and pluviometry.
There are mainly two different types of corrosion test standards, field performance and accelerated corrosion tests. Cotec Labs is focused on different types of standardized corrosion tests.
What is important when choosing a test method is to make sure the controlled environment matches the natural outside environment in terms of behaviour of the protective coating when it degrades. Since the methods used in a laboratory environment are accelerated, studies must underpin the extrapolation of test duration.
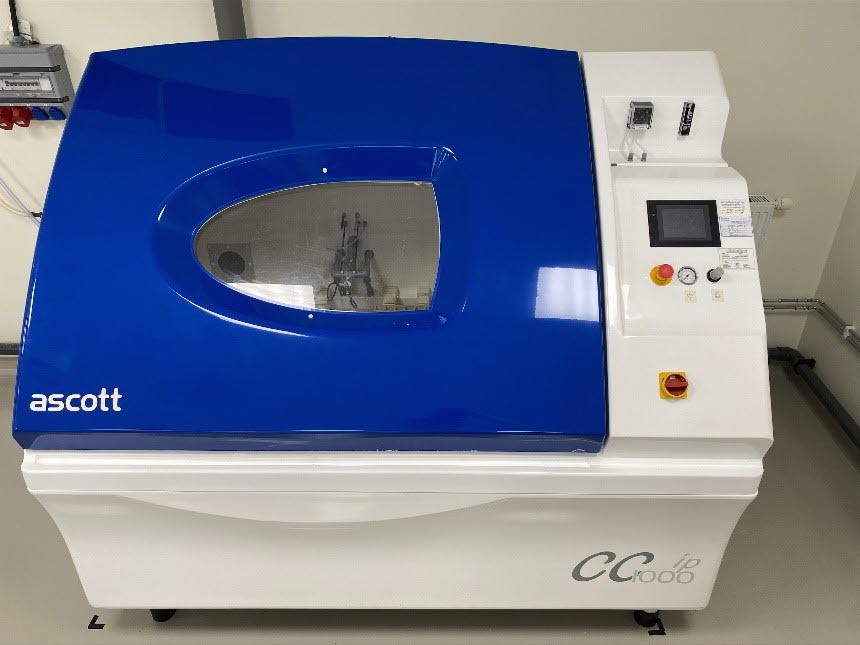
Test principle VW PV 1209
The VW PV 1209 test method is designed to assess the corrosion resistance of metallic materials and coatings used in automotive components. The test simulates real-world environmental conditions that vehicles might encounter during their operational life. The principle of the VW PV 1209 test cycle involves subjecting test specimens to a combination of corrosive agents, such as salt spray (EN ISO 9227), humidity, and temperature variations, to accelerate the minor selective corrosion process and evaluate the durability of the materials. The tests can be used for verification of painted component or for example a cooling fin or water radiators made of aluminum alloys with a brazed surface.
The key principles of the test method are as follows:
- Accelerated Corrosion Exposure: The test cycle exposes metallic specimens to aggressive environmental conditions that accelerate the natural corrosion load process. This acceleration allows manufacturers to observe and assess the effects within a relatively short period, providing insights into long-term performance.
- Simultaneous Pressure Load: The following test cycle recreates conditions such as salt spray, humidity, and temperature fluctuations that vehicles encounter in different regions and seasons.
- Assessment: Technicians monitor the required test specimens over a specified duration, observing the appearance and progression of corrosion.
- Documentation of Results: The standard specifies that the observations, ratings, measurements, and photographs are compiled into a comprehensive report. This report details the test conditions, exposure duration, test results, and any relevant notes from the evaluation process.
- Certification and Compliance: Materials and coatings that successfully pass the VW PV 1209 test cycle and align with the established criteria are certified as corrosion-resistant. This certification ensures that the automotive components made from these materials can withstand corrosive environments and contribute to the overall durability of vehicles.
Test evaluation VW PV 1209
ASTM B117 salt spray test standard is a test method for salt spray (fog) exposure that is widely used to evaluate the corrosion resistance of materials and surface coatings. Here are some of the uses and factors to consider:
- Visual Inspection: Technicians visually examine the individual components, for example water radiators, for visible signs of irregularities, including rust formation, discoloration, pitting etc. This initial inspection provides a qualitative assessment of the extent of corrosion.
- Photographic Documentation: Detailed photographs are taken of the test specimens before and after exposure to the conditions. These images of the finished part serve as visual records and facilitate a side-by-side comparison of the specimens’ condition at different stages of the test.
- Corrosion Resistance Rating: The extent of the specimens is often rated on a scale or categorized into different levels based on predefined criteria that the standard specifies. These ratings help standardize the evaluation process and provide a clear indication of the specimens’ corrosion resistance performance.
In summary, the evaluation of the required cycle times involves a comprehensive analysis of the test samples’ condition, comparing the results to technical supply specifications. The evaluation process provides valuable insights for manufacturers to make informed decisions about materials, coatings, and design improvements, ultimately leading to the production of vehicles with enhanced durability and longevity. VW PV 1210 or EN ISO 6270 are also very helpful tests corrosion resistance standards, together with adhesion testing with example cross cut (EN ISO 2409) stone chip testing or high water pressure testing.
Our most common corrosion tests
Talk to our corrosion test experts
Are you interested in conducting a test? Feel free to contact us – we’re here to assist you every step of the way.
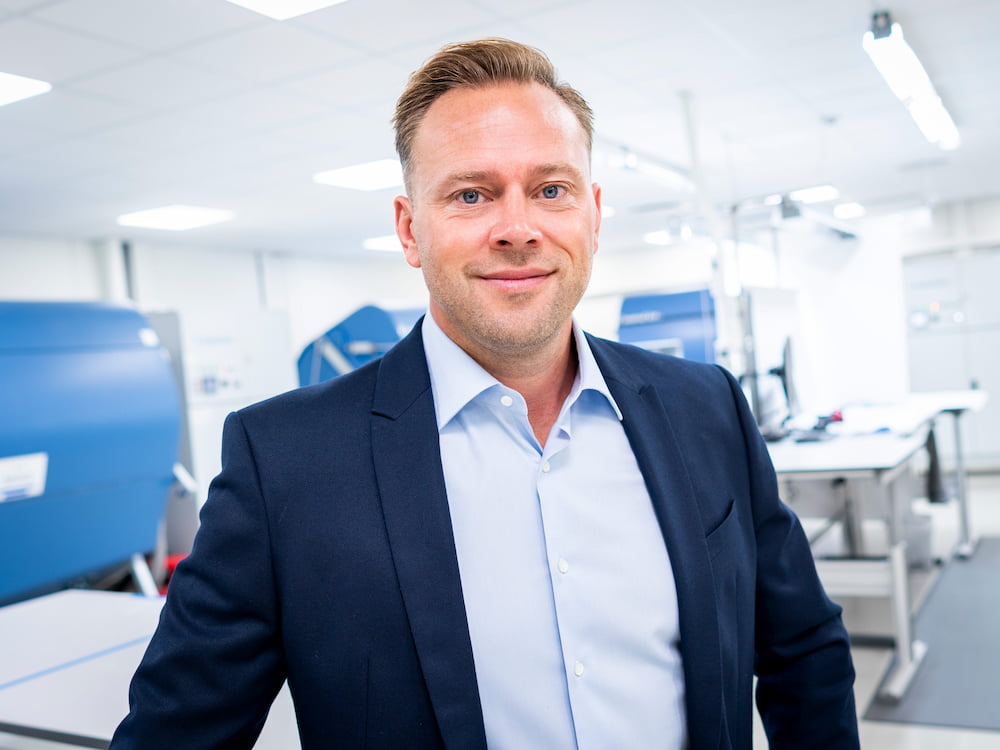
Joakim Ekström
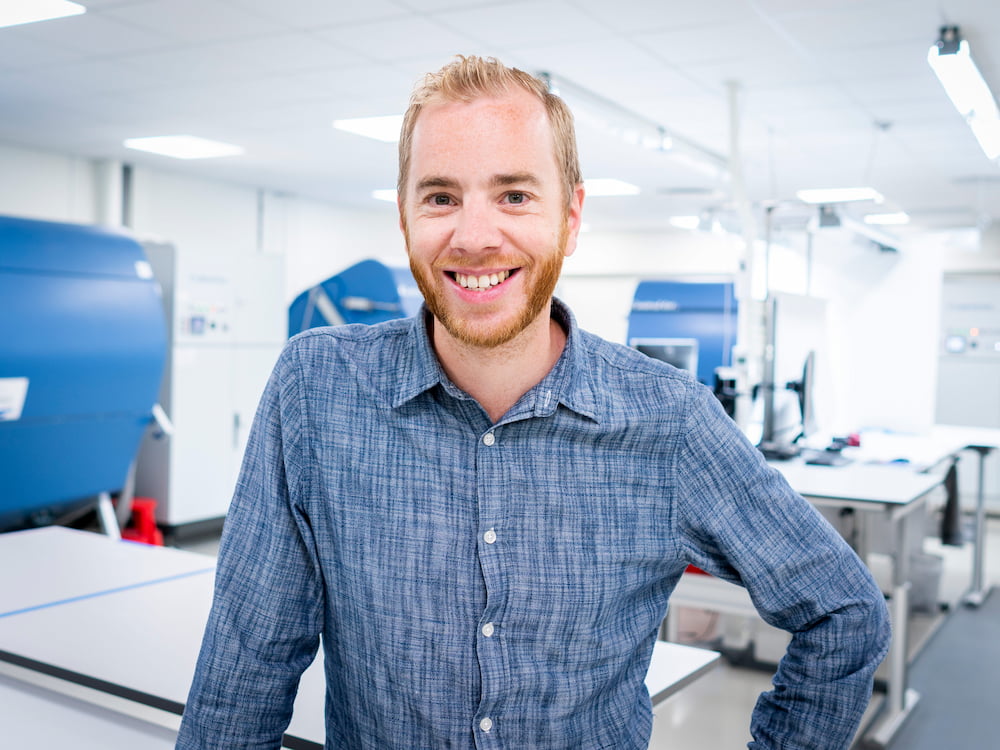
Erik Waltersson
Accredited by SWEDAC
and part of the international accreditation network ILAC
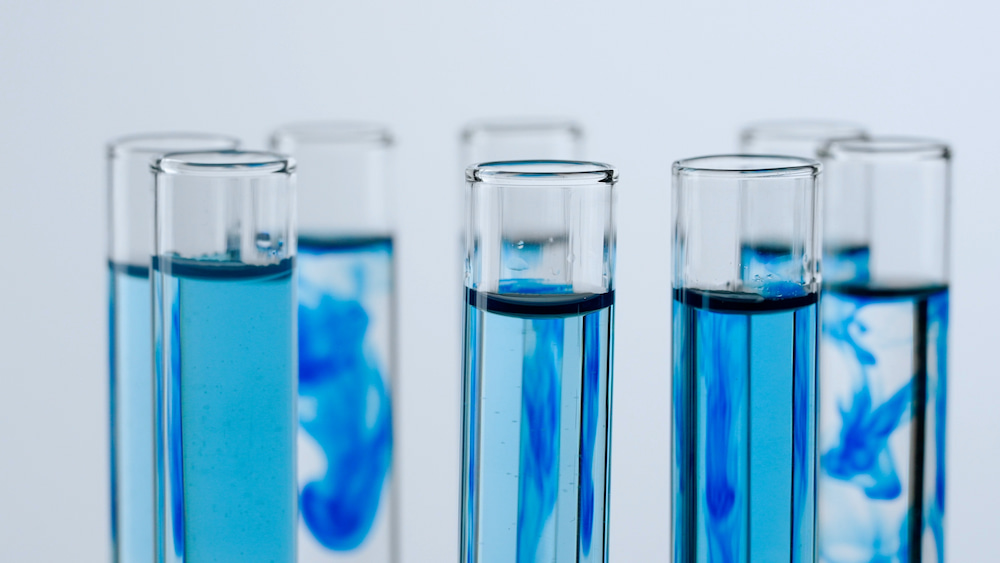
Methods and requirements
We offer a comprehensive and continuously expanding lab-scope of over 300 available test methods and standards.
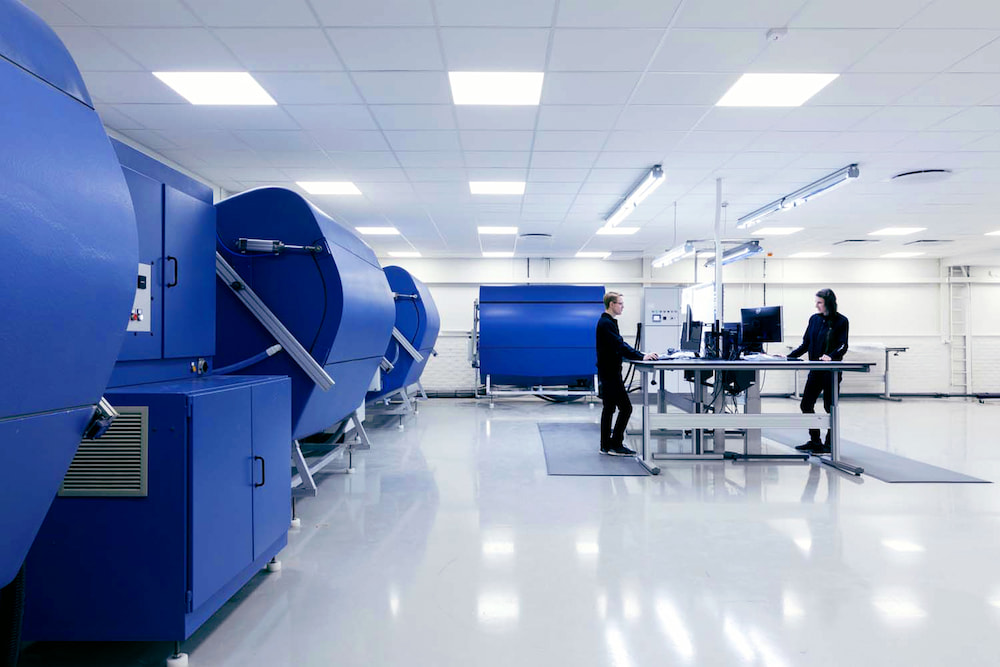
Laboratory and equipment
Cotec Labs provides a 1200 sqm laboratory facility. Take a closer look at our laboratory
and equipment.
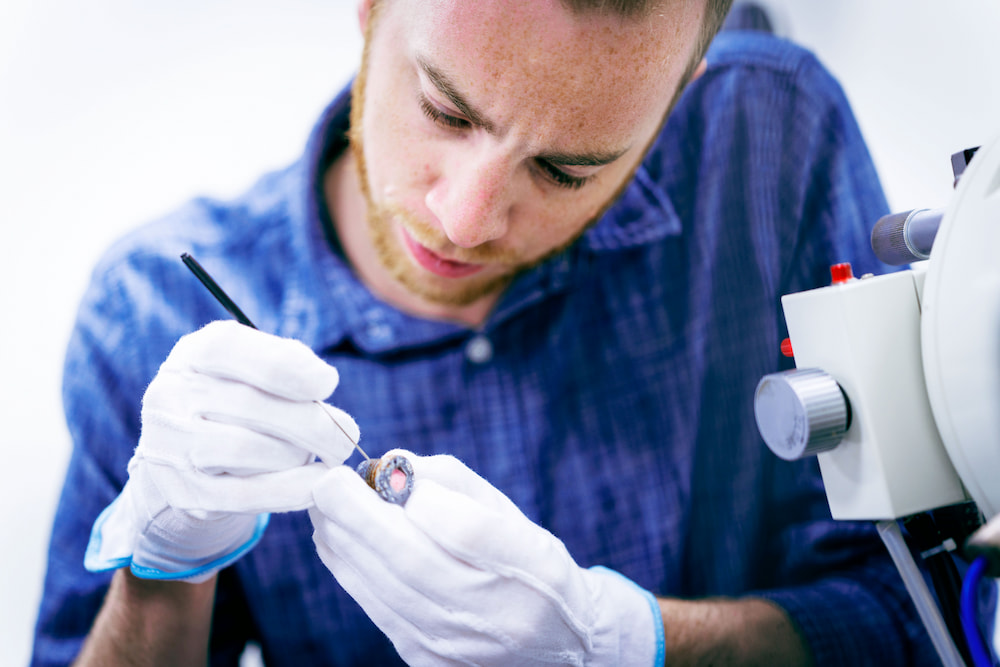
Quality and certificates
We are accredited by Swedac and part of the international accreditation network ILAC.