Methods & requirements
VW PV 1210 Corrosion test
Corrosion testing determines the resistance of materials to corrosion under specific environmental conditions, like temperature and humidity. Other accelerating factors can be presence of chemicals and the pH-level of the salt fog and pluviometry.
There are mainly two different types of corrosion test standards, field performance and accelerated corrosion tests. Cotec Labs is focused on different types of standardized corrosion tests.
What is important when choosing a test method is to make sure the controlled environment matches the natural outside environment in terms of behaviour of the protective coating when it degrades. Since the methods used in a laboratory environment are accelerated, studies must underpin the extrapolation of test duration.
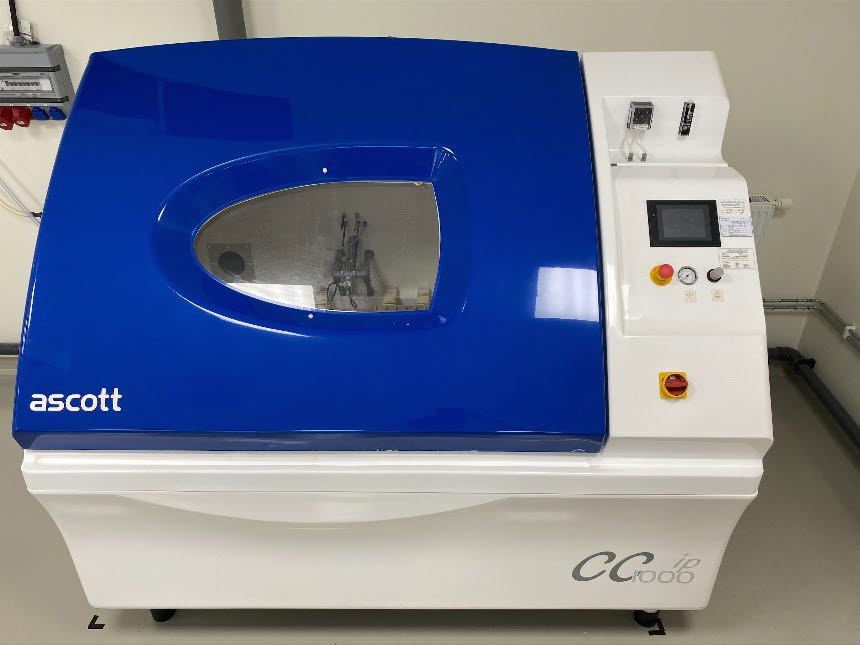
Test cycle principles, VW PV 1210
VW PV 1210 is a complete testing used by Volkswagen Group to evaluate the durability of materials and manufacturing operations used in automotive bodies applications and standard production tests. The following are the principles of this test method:
Purpose
The purpose of the VW PV 1210 test sequence is to evaluate the durability of materials and components under simulated real-world conditions.
Test specification
The PV 1210 test conditions simulate various environmental conditions such as temperature, humidity, vibration, and mechanical stress, that the materials and components may encounter during their service life.
Test specimens
Test specimens are prepared according to specified dimensions and shapes that represent the real-world application of the different anti corrosion coatings, metallic base material, fully painted bodies or component. If needed it can be acquired to completely covered unprotected trim edges.
Test equipment
The test equipment used in this non destructive thermographic method includes various instruments such as thermal chambers and environmental chambers.
Test procedure
The test procedure involves subjecting the differing anti corrosion coatings to a series of defined corrosion conditions and rest phases for a specified duration of time. The specimens are evaluated at regular intervals during the test to determine any changes in their mechanical, physical, or chemical properties.
Test results
The test results are used to evaluate the durability of the material or component under test and to make any necessary design or material changes to improve the durability of the final product. Examples of this is quantitative specific evaluation regarding surface or edge corrosion.
Test report
The test report includes detailed information about the test conditions, test specimens, test equipment, test procedure, and test results. The report is used to document the test method and to communicate the results to interested parties.
Salt spray phase, VW PV1210
The salt spray cycle of VW PV 1210 test is a test procedure that simulates the effects of saltwater exposure and humid aging on anti corrosion coatings and components used in automotive applications. This test phase is designed to evaluate the resistance of materials and components to corrosion caused by saltwater exposure.
The salt spray test involves subjecting the horizontal positioned test specimens to a static load of fine mist of saltwater, humid aging and constant elevated temperature for a specified duration of time, in salt spray test chambers. The specimens are placed in a chamber that simulates the conditions of a saltwater environment. The test specimens are typically made of metal, plastic, or coated materials.
During the test cycles, the specimens or body test panels are periodically evaluated to determine any changes in their appearance or properties. The evaluation may include visual inspection, weight measurements, corrosion curves and other tests to determine the extent of corrosion or damage.
The VW PV 1210 salt spray phase typically lasts for a minimum of 24 hours and may be extended up to several hundred hours depending on the application and requirements. The test results are used to evaluate the corrosion mechanism of the materials or components to saltwater exposure and to make any necessary design or material changes to improve their performance.
The salt spray phase is an important test procedure to ensure that anti corrosion coatings and components used in automotive applications can withstand the harsh conditions of saltwater environments, such as coastal areas or areas with winter road salt.
The component testing phase is important to ensure that individual components used in automotive applications meet the required durability and performance standards, and to evaluate the corrosion behavior. The results of the component testing are used to identify any weaknesses or areas of improvement in the design or material selection of the components, to avoid that base metal corrosion, rust creep, corrosion perforations or surface corrosion occur. This information can then be used to make any necessary changes to improve the performance and durability of the final product.
Our most common corrosion tests
Talk to our corrosion test experts
Are you interested in conducting a test? Feel free to contact us – we’re here to assist you every step of the way.
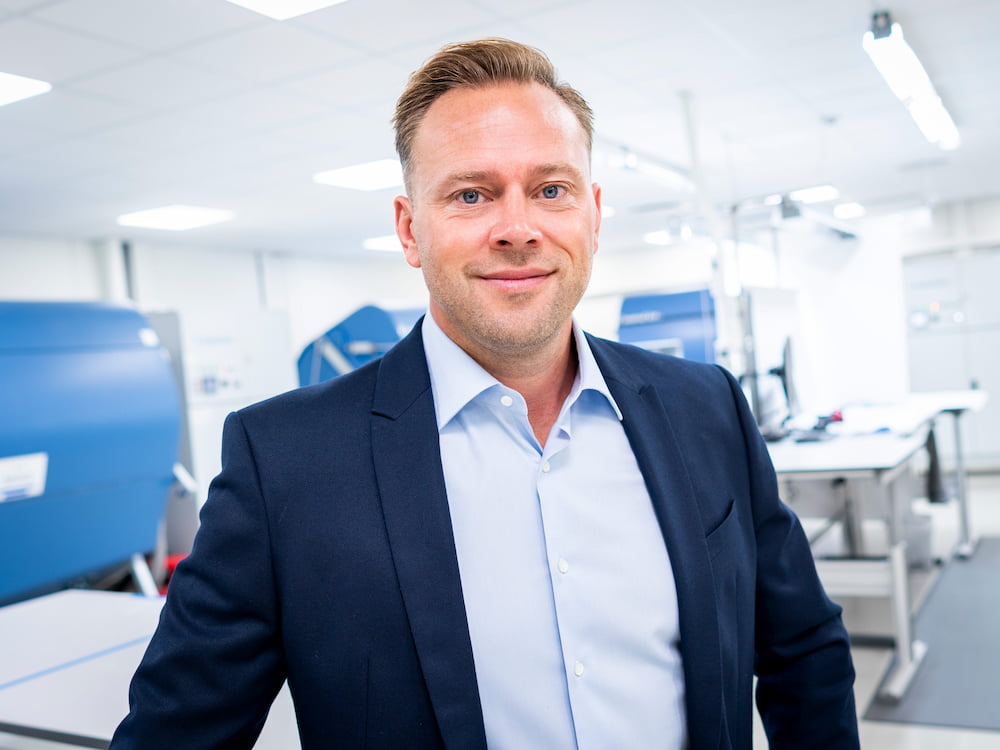
Joakim Ekström
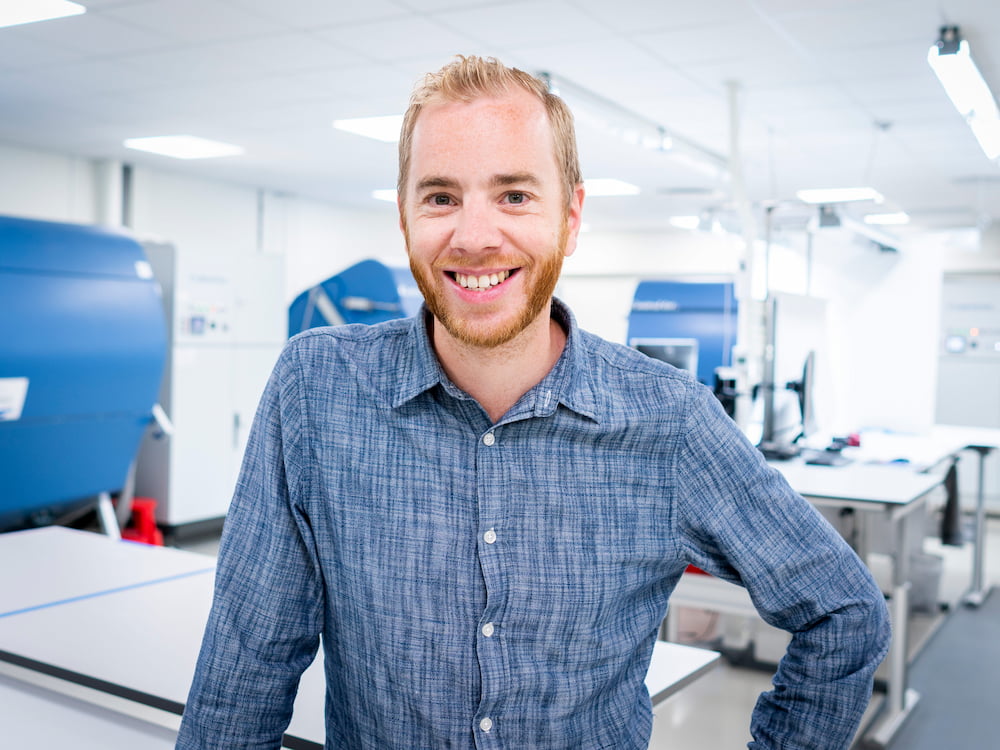
Erik Waltersson
Accredited by SWEDAC
and part of the international accreditation network ILAC
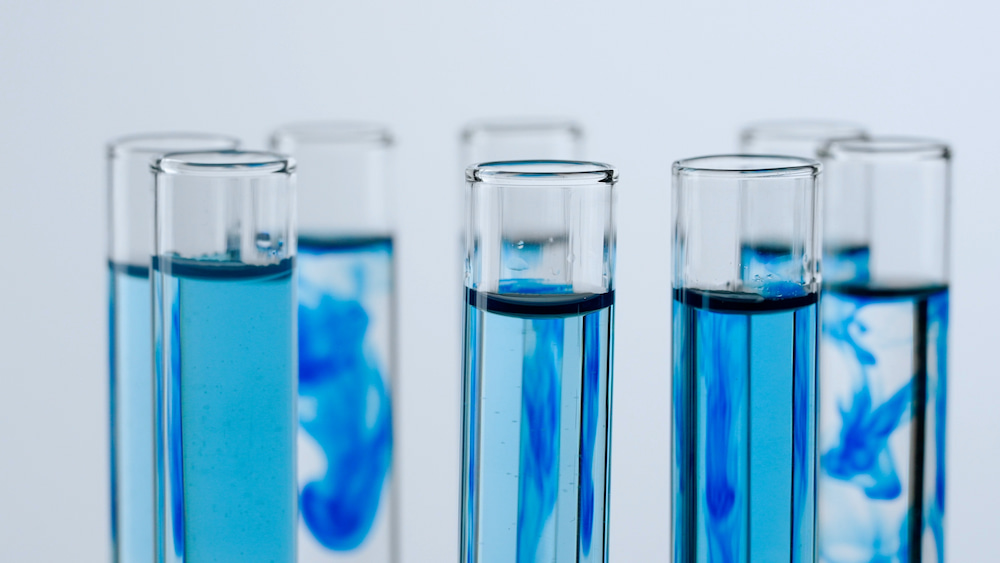
Methods and requirements
We offer a comprehensive and continuously expanding lab-scope of over 300 available test methods and standards.
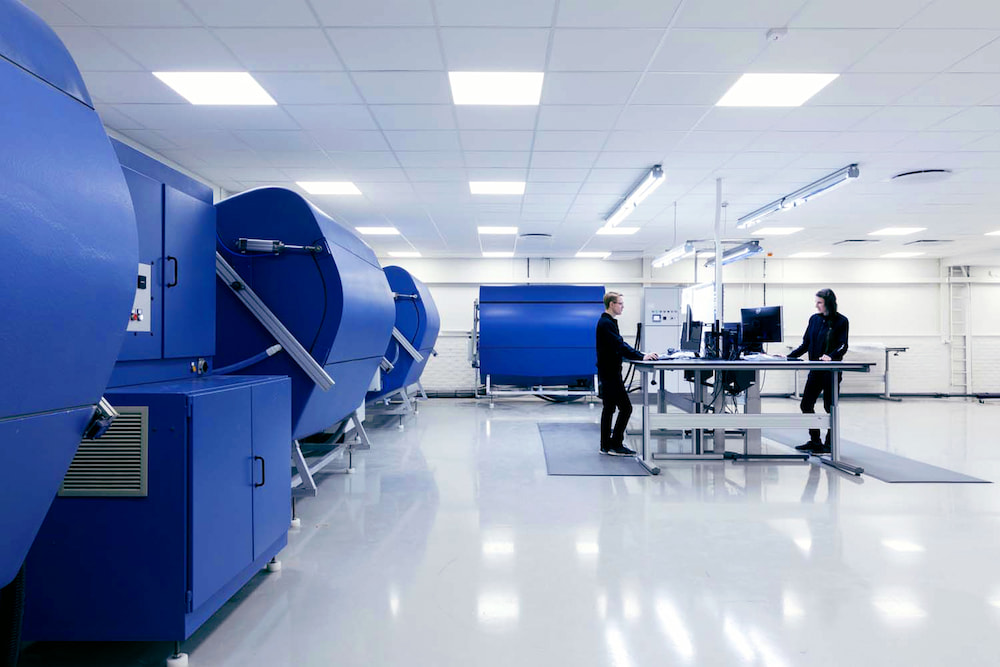
Laboratory and equipment
Cotec Labs provides a 1200 sqm laboratory facility. Take a closer look at our laboratory
and equipment.
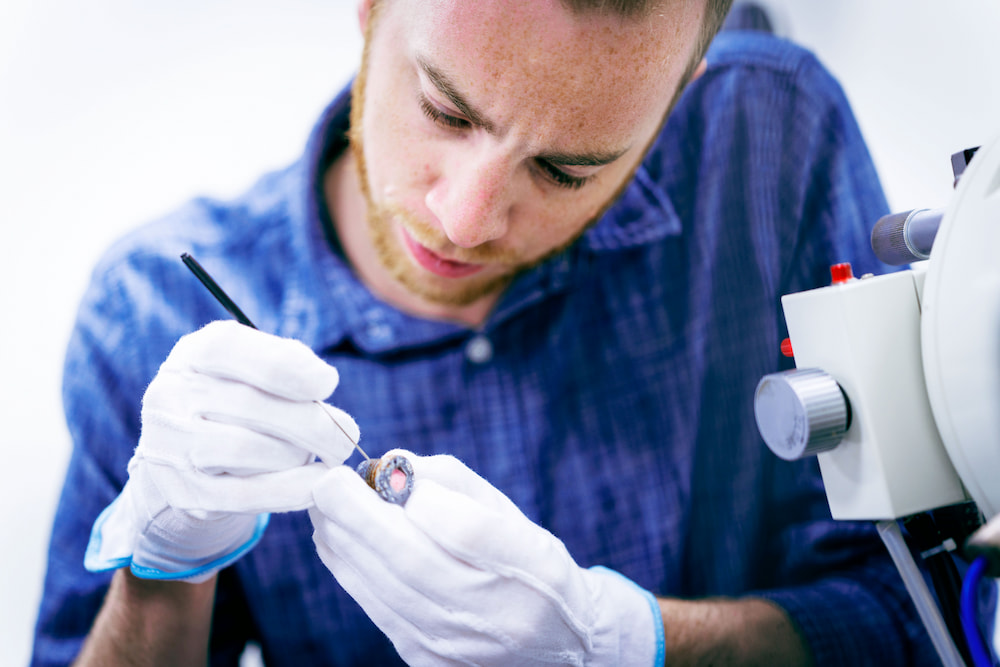
Quality and certificates
We are accredited by Swedac and part of the international accreditation network ILAC.