Methods & requirements
ASTM B117 Salt Spray Test
Corrosion testing determines the resistance of materials to corrosion under specific environmental conditions, like temperature and humidity.
Other accelerating factors can be the presence of chemicals and the pH-level of the salt fog and pluviometry, which are critical parameters outlined in ASTM B117 for salt spray tests.
When selecting a test method, ensuring the controlled environment matches natural outside conditions is crucial for accurate evaluation of protective coating degradation behavior.
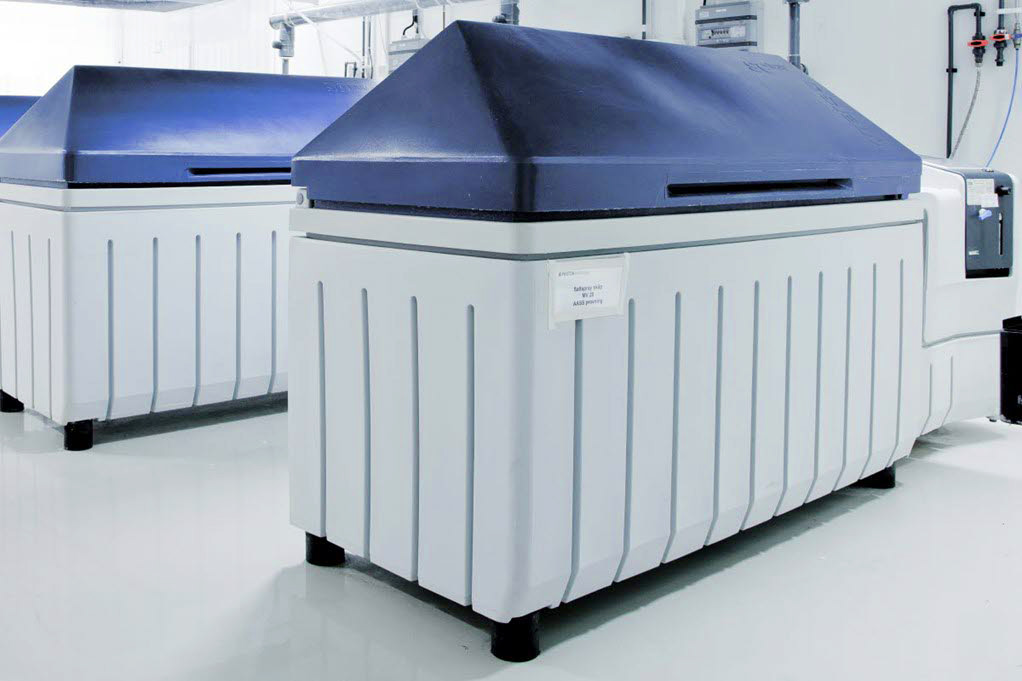
What is Salt Spray Testing?
Salt spray testing, also known as salt fog testing, is a standardized corrosion test method used to evaluate the corrosion resistance of materials and surface coatings.
This test involves exposing coated samples to a controlled corrosive environment, typically within a salt spray cabinet, to produce relative corrosion resistance information. By simulating the effects of natural environments, such as coastal or marine atmospheres, salt spray testing provides an accelerated means of assessing how coated metals will perform over time.
Widely utilized across various industries – including automotive, aerospace, and construction—salt spray testing helps determine the suitability of coatings for use as protective finishes. The test’s ability to replicate harsh environmental conditions makes it an invaluable tool for predicting the longevity and effectiveness of corrosion-resistant coatings.
What is ASTM B117 test?
ASTM B117 is a widely used standard that provides a test method for evaluating the corrosion resistance of metallic materials. The standard is maintained by ASTM International, an organization that develops and publishes voluntary consensus technical standards for a wide range of materials, products, systems, and services. This standard practice for operating salt spray fog apparatus is essential for manufacturers, researchers, and professionals involved in the production, testing, and use of metallic materials.
The primary purpose of salt spray tests, as outlined in ASTM B117, is to provide a uniform and reproducible test method for determining the corrosion resistance of materials.
The standard specifies conditions for conducting a salt spray (fog) test, which exposes the test specimen to a corrosive test environment by spraying it with a salt water solution. The test is designed to simulate the corrosive effects of exposure to salt-laden atmospheres, such as those found in marine environments, and to provide a means of evaluating the suitability of materials for use in such highly corrosive test environments.
ASTM B117 Test Procedure
The ASTM B117 test procedure involves operating a salt spray apparatus to create a controlled corrosive environment for testing metals and coated metals. This environment is designed to produce relative corrosion resistance information for specimens, providing valuable insights into their durability. The test procedure includes several key steps:
- Preparation of the test specimens – Test specimens are meticulously prepared according to the test requirements, which include cleaning and drying to ensure no contaminants affect the results.
- Exposure to salt spray – The prepared specimens are then exposed to a continuous indirect spray of a salt water solution within a salt spray cabinet. This exposure simulates the corrosive effects of salt-laden atmospheres.
- Maintenance of the test environment -Throughout the test, the environment is maintained at a controlled temperature and humidity level to ensure consistent and reliable test conditions.
- Evaluation of corrosion resistance – After a predetermined period, typically ranging from 24 to 96 hours, the corrosion resistance of the test specimens is evaluated. This evaluation can involve visual inspection or measuring the mass loss of the specimens.
- Interpretation of results – The final step involves interpreting the test results to determine the relative corrosion resistance of the specimens. This information is crucial for predicting how the materials and coatings will behave in natural environments.
The ASTM B117 test procedure is a cornerstone in the coatings industry, providing a standardized method to evaluate the performance of protective coatings. However, it is important to recognize that while salt spray testing offers valuable data, it has limitations and may not always predict performance in natural environments accurately.
ASTM B117 Uses and Applications
ASTM B117 salt spray test standard is a method for salt spray (fog) exposure that is widely used to evaluate the corrosion resistance of materials and surface coatings. The testing procedure offers valuable insights for various applications:
Primary uses:
- Qualifying protective coatings and materials – The test method is used to test the resistance of coatings and materials to salt spray tests and other corrosive agents. This testing helps manufacturers ensure their products will perform well in real-world conditions.
- Quality control – ASTM B117 testing procedure verifies that coatings and materials meet specific performance requirements. It can also help identify problems with manufacturing processes or materials.
- Research and development – The test method is often used in research and development to evaluate the effectiveness of new coatings and materials to resist corrosion.
Operating Salt Spray Fog Test Parameters
The standard practice for operating salt spray fog apparatus requires specific testing conditions. The typical experimental parameters for the ASTM B117 salt fog test include:
- Test duration – The test duration for ASTM B117 salt spray is typically 24 to 72 hours, depending on the material being tested and the desired level of corrosion resistance. Exposure periods may be extended to several hundred hours for certain applications.
- Test solution – The test solution used in ASTM B117 salt spray is a 5% salt water solution, prepared by dissolving sodium chloride (NaCl) in distilled water. The pH of the solution is maintained between 6.5 and 7.2 (neutral pH).
- Test temperature – The chamber temperature for ASTM B117 is maintained at 35°C ± 2°C (elevated temperature).
- Humidity – The humidity of the test chamber is maintained at 95% ± 5%.
- Spray rate – The spray rate in ASTM B117 is typically set at 1.0 to 2.0 ml per hour per square meter of surface area, using pressurized air for continuous indirect spray distribution.
These parameters are essential for ensuring the reliability and consistency of salt spray tests as outlined by ASTM B117.
Test Specimen Preparation and Evaluation
Proper preparation of test specimens is crucial for obtaining reliable results from salt spray testing:
- Sample preparation – The test specimen must be cleaned and prepared properly before testing to ensure accurate results. Any contaminants on the surface of the sample can affect the salt spray results.
- Positioning in chamber – Specimens tested must be positioned in the enclosed chamber to ensure uniform exposure to the salt spray fog.
- Sufficient replicates – Testing should include sufficient replicates to ensure statistical validity of results.
- Evaluation criteria – The specimens are evaluated for corrosion after the test period. The evaluation is done by visual inspection or by measuring the mass loss of the specimen. A typical result of ASTM B117 salt spray is a rating based on the severity of corrosion, with ratings ranging from 0 (no corrosion) to 10 (severe corrosion).
Modified Salt Spray Testing Approaches
While the standard ASTM B117 salt spray test provides valuable data, modified salt spray testing approaches can offer additional insights:
Acetic acid-salt spray test
This modification includes acetic acid in the solution to create a more aggressive test environment.
Cyclic corrosion testing
This approach alternates between salt spray exposure and dry conditions to better simulate natural environments.
Salt spray testing with different coatings
Comparing the performance of different coatings under identical conditions can provide relative corrosion resistance information.
Limitations of B117 Salt Spray Test
While ASTM B117 salt spray is a widely used test method, it has some limitations to consider:
Correlation with natural environments
The test may be a rapid but unreliable means of predicting coating behavior in natural environments. While salt spray tests provide valuable data, they have limitations and may not always predict performance in natural environments accurately.
Comparison limitations
Results from similar specimens tested in different fog chambers or under nominally similar conditions may not be comparable.
Environmental factors
The test does not simulate all types of corrosion environments, such as those with acidic or alkaline solutions, and it does not consider the effects of UV radiation or other environmental factors.
Specific product limitations
The standard does not prescribe the type of test specimen or exposure periods to be used for a specific product.
Interpreting Salt Spray Results
Interpreting the results of ASTM B117 salt spray must be done correctly to determine the level of corrosion resistance of the coating or material being tested:
Visual inspection
Evaluate the appearance of corrosion products (red rust or other oxides) after the predetermined test duration.
Coating adhesion
Assess how well the coating adheres to the substrate after exposure.
Relative corrosion resistance
Compare the performance of coated metals exposed to the same conditions to produce relative corrosion resistance information.
Corrosion resistant rating
Determine if the material or coating meets the required standards to be considered corrosion resistant for its intended application.
International Standards and Equivalents
ASTM B117 salt spray test is one of several internationally recognized principles for corrosion testing:
ASTM International
Besides B117, ASTM International offers other related standards such as ASTM G85.
ISO standards
ISO 9227 provides similar methods for salt spray testing.
Regional standards
Various countries have developed their own standards based on similar testing concepts. ASTM B117 salt spray tests are recognized internationally and have equivalents in other standards such as ISO 9227.
Ensuring Reliable Testing Results
To ensure reliable results from your ASTM B117 salt spray testing program:
Calibrated equipment
Ensure your salt spray cabinet and all operating variables are properly calibrated.
Controlled corrosive
environment
Maintain consistent testing conditions throughout the test duration.
Trained personnel
Ensure that tests are conducted by personnel familiar with the standard practice for operating salt spray fog apparatus.
Documentation
Maintain detailed records of all testing parameters and results for proper evaluation criteria selected.
By understanding the proper application and limitations of the ASTM B117 salt spray test, you can effectively evaluate the corrosion performance of your materials and coatings, leading to better product development and quality control decisions.
Frequently Asked Questions About ASTM B117
What is ASTM B117?
ASTM B117 is a widely used standard that provides a test method for evaluating the corrosion resistance of metallic materials. The standard is maintained by ASTM International and provides a uniform and reproducible test method for determining corrosion resistance by exposing specimens to a corrosive environment using salt spray.
What are the test conditions for ASTM B117?
The ASTM B117 test requires specific conditions: temperature maintained at 35°C ± 2°C, humidity at 95% ± 5%, and a 5% salt water solution with pH maintained between 6.5 and 7.2. The spray rate is typically set at 1.0 to 2.0 ml per hour per square meter of surface area.
How long does an ASTM B117 test take?
Test duration for ASTM B117 salt spray is typically 24 to 72 hours, depending on the material being tested and the desired level of corrosion resistance. Exposure periods may be extended to several hundred hours for certain applications.
What industries use ASTM B117 testing?
ASTM B117 is widely utilized across various industries including automotive, aerospace, and construction to determine the suitability of coatings for use as protective finishes.
How are ASTM B117 test results evaluated?
Specimens are evaluated for corrosion after the test period through visual inspection or by measuring the mass loss of the specimen. A typical result is a rating based on the severity of corrosion, with ratings ranging from 0 (no corrosion) to 10 (severe corrosion). Using evaluation as per ISO 10289 the numerical rating is preceded by Rp and A. Rp means rust protection (red rust). A stands for appearance, obtained by oxidation of a sacrificial metal like Zn, leaving white corrosion on the surface.
What are the main uses of ASTM B117 testing?
The test method is used for qualifying protective coatings and materials, quality control to verify that coatings meet specific performance requirements, and research and development to evaluate the effectiveness of new coatings and materials. The method’s primary application is comparative testing and process control.
What are the limitations of ASTM B117 testing?
ASTM B117 may be a rapid but unreliable means of predicting coating behavior in natural environments. The test does not simulate all types of corrosion environments, such as those with acidic or alkaline solutions, and doesn’t consider the effects of UV radiation or other environmental factors.
Are there alternatives to standard ASTM B117 testing?
Yes, modified approaches include acetic acid-salt spray tests (AASS) that create a more aggressive environment, and cyclic corrosion testing that alternates between salt spray exposure and dry conditions to better simulate natural environments.
How does ASTM B117 compare to other international standards?
ASTM B117 has international equivalents such as ISO 9227 (NSS). ASTM International also offers other related standards such as ASTM G85.
What specimen preparation is required for ASTM B117?
Test specimens must be cleaned and prepared properly before testing to ensure accurate results, as any contaminants on the surface can affect the salt spray results. Specimens must be positioned in the enclosed chamber to ensure uniform exposure to the salt spray fog. The rinsing and dying procedures are also of great importance before the final evaluation.
Our most common corrosion tests
Talk to our corrosion test experts
Are you interested in conducting a test? Feel free to contact us – we’re here to assist you every step of the way.
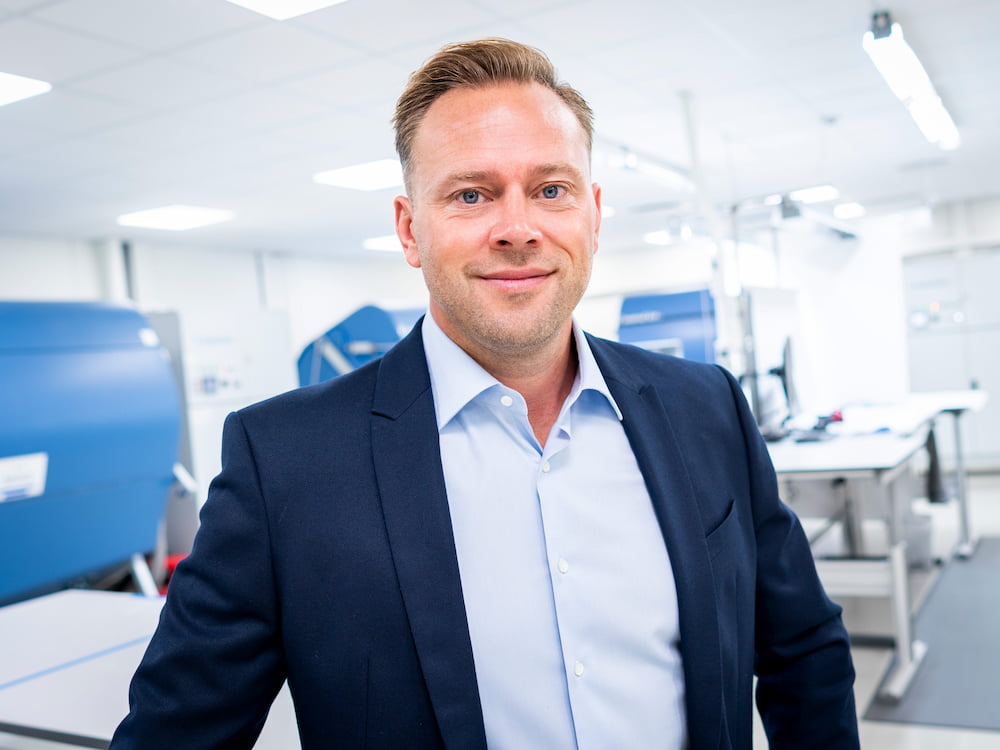
Joakim Ekström
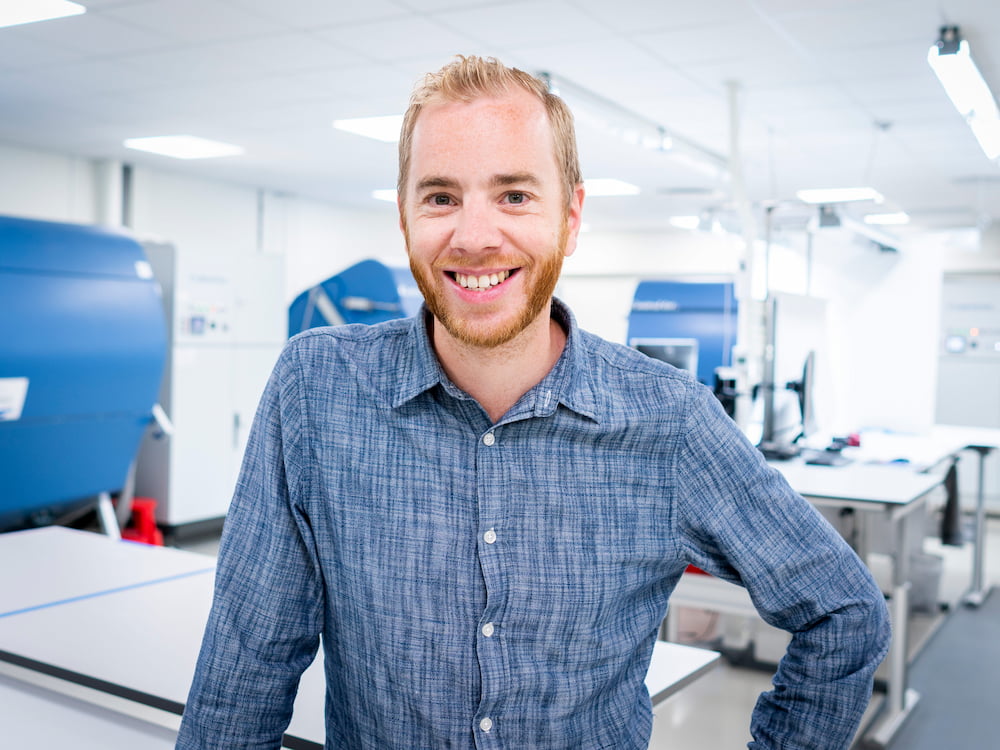
Erik Waltersson
Accredited by SWEDAC
and part of the international accreditation network ILAC
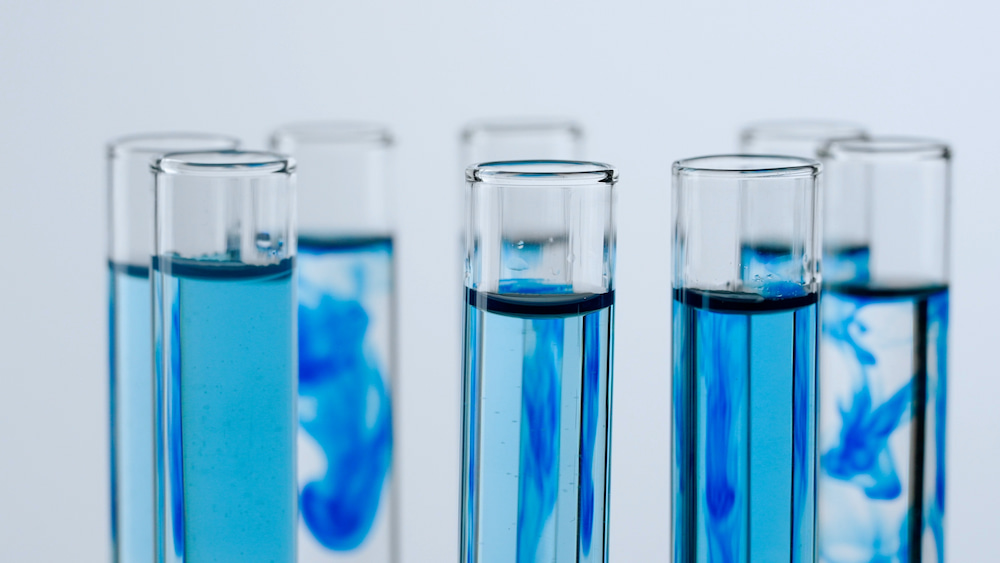
Methods and requirements
We offer a comprehensive and continuously expanding lab-scope of over 300 available test methods and standards.
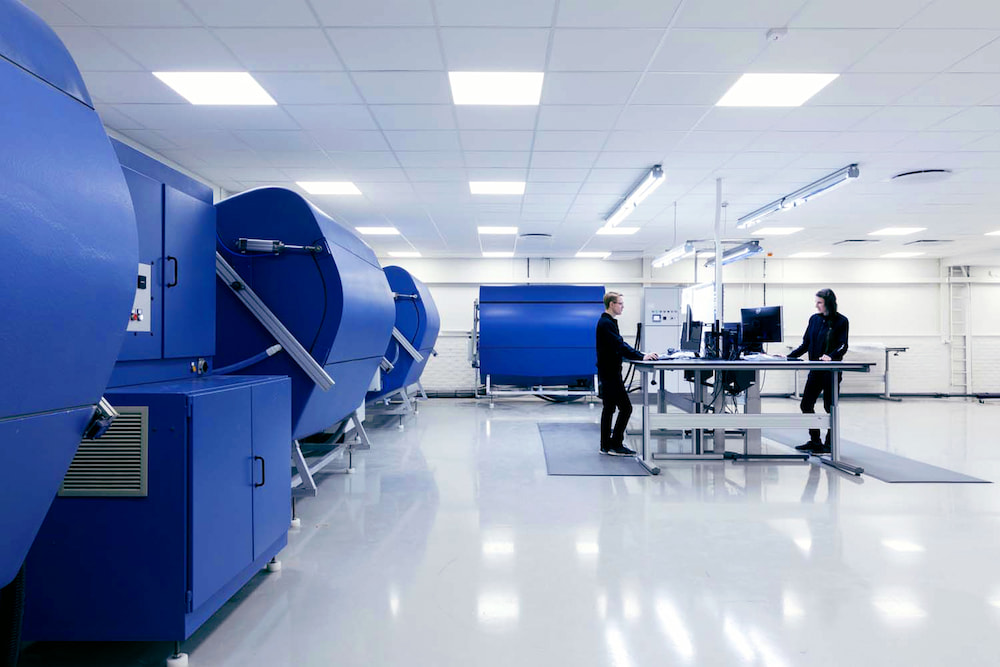
Laboratory and equipment
Cotec Labs provides a 1200 sqm laboratory facility. Take a closer look at our laboratory
and equipment.
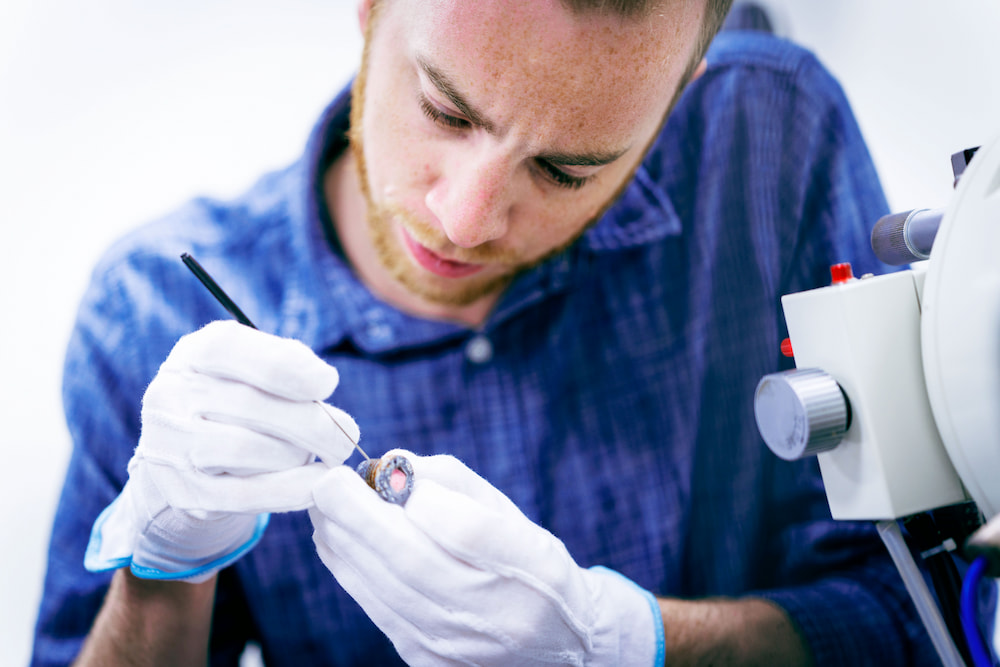
Quality and certificates
We are accredited by Swedac and part of the international accreditation network ILAC.